WORKS
導入事例

株式会社不二越
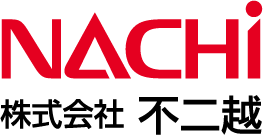
株式会社不二越 様
屋内測位技術でボトルネックの把握と改善を実現
株式会社不二越 ロボット事業部 ロボット製造所工程進捗の見える化でPDCAサイクルを素早く回す
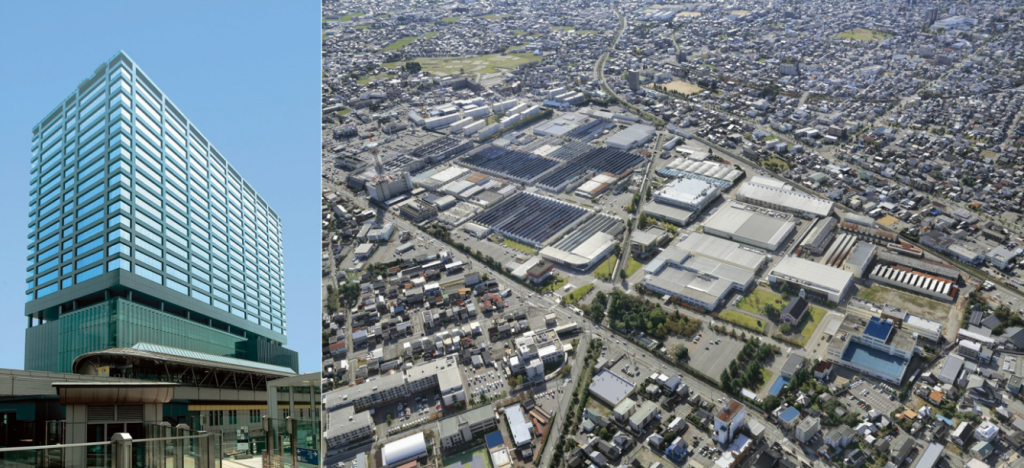
株式会社不二越のロボット事業部ロボット製造所では、従来の生産進捗管理システムが、複数の工程をブロック括りで管理する仕組みだったことから、単一工程ごとの進捗の把握に時間がかかり、対応が遅れるという課題を抱えていた。同製造所では改善にあたりiField indoor を導入、すべての仕掛品の位置を見える化することで、ボトルネックとなっている工程を把握し、作業フローやレイアウトを最適化することでKPI 指標を改善することに成功している。
iField indoor の導入で工程ごとの仕掛品の状況を把握
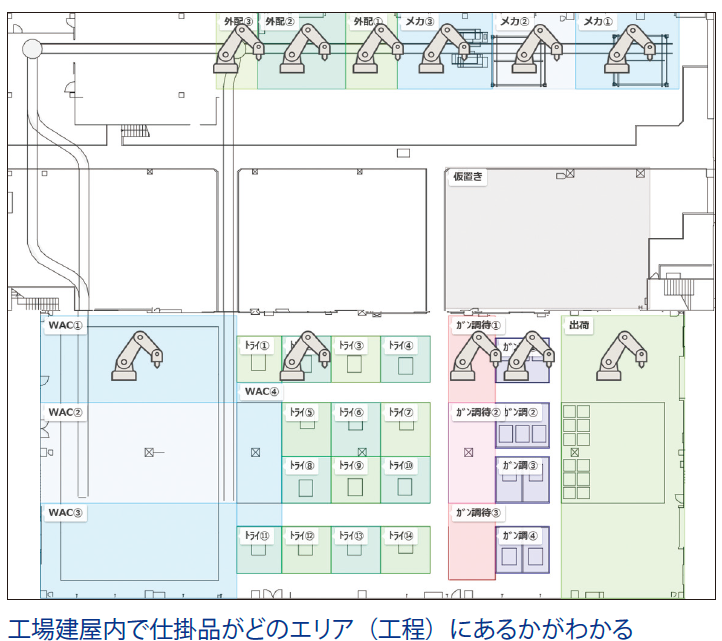
同製造所では利用していた生産進捗管理システムが複数の工程をブロックで括って管理する仕組みだったことから、単一の工程の状況を把握するには管理者が毎回現場を確認しに回る必要があり、その業務負荷に加え、対応にタイムラグが生じるという課題があった。そこで改善のための方策として、単一工程ごとの進捗を把握するにあたり、屋内測位による位置情報を利用することを立案した。
屋内測位の方式として、測位対象となる人やものがスマートフォン等の端末で電波を受信して位置を計算し、クラウドにアップロードされて共有されるスマートフォン位置推定型測位と、測位対象にビーコンをつけて電波を発信し、ゲートウェイがそれを受信してクラウドにアップロードした後に位置を計算して共有するゲートウェイ位置推定型測位の2つの選択肢があった。同製造所では測位対象が多いことから、比較的安価であり、長時間稼働も可能なビーコンによるゲートウェイ位置推定型測位を採用する形でiField indoorを導入し、測位対象となる仕掛品(ロボット)にビーコンをつけることで位置を把握し、工程進捗の見える化を行った。
先頭工程の作業者がスマートフォンの操作により、ビーコンと取り付けられた仕掛品の製造番号を紐づけて登録することで、その仕掛品がどの工程にあるのかがiField indoorの画面上で見える化される。そして全工程を終えた製品は出荷前にビーコンが取り外され、紐づけは解除される。ビーコンは先頭工程に戻って再利用されるという仕組みだ。
「ユーザーインターフェースは現場のニーズを反映してシンプルなものとなっています。マップ上で色分けされたエリア(工程)ごとに、何台の仕掛品があるかわかるほか、どの製造番号のロボットが現在どの工程にあるのかが一覧で見られる測位中リストから検索を行うことも可能です」(株式会社不二越 ロボット事業部 ロボット製造所 臼井竜彦氏)
改善の結果をすぐにデータに反映することで次の改善につながる
ロボットの製造工程は、①メカ組立工程→②機体内配線工程→③オプション組付工程→④動作試験・検査工程→⑤サーボガン取付・調整工程→⑥出荷待ちと進んでいく。iFieldindoorの画面でヒートメッシュを表示させたところ、①②工程のエリアには赤で表示される停滞が見られなかったのに対して、③以降の工程には停滞が確認された。
実際にどれくらい停滞しているのかを把握するために、標準作業時間と実際の時間の差分をグラフにより可視化してみると、③のオプション組付工程で長く停滞していることがわかった。その原因について、臼井氏は「オプション組付工程はお客様に応じて使う部品が異なり、組立計画と同調しないことがあります。その場合オプション組付を飛ばして先に動作試験・検査工程を実施してから戻るというように、③と④の工程を行ったり来たり繰り返すようなことがありました。また、オプション組付工程は事前の段取りに時間がかかることも遅れの原因となっていました」と分析する。
この結果を受けて、同製造所では工程の順序を組み替えることで対応することとした。オプション組付工程の前に動作試験・検査工程を持ってきて、導線改善のためのレイアウト変更も行ったところ、全体の流れが改善された。
「改善結果がすぐにデータに反映されるので、次に何を改善すればいいのかがわかる。製造現場と話し合いながらどんどん改善が進むのがiField indoorの強みです」(株式会社不二越ロボット事業部ロボット製造所 所長 林雅樹氏)
作業者の位置情報を把握することで働き方改革も
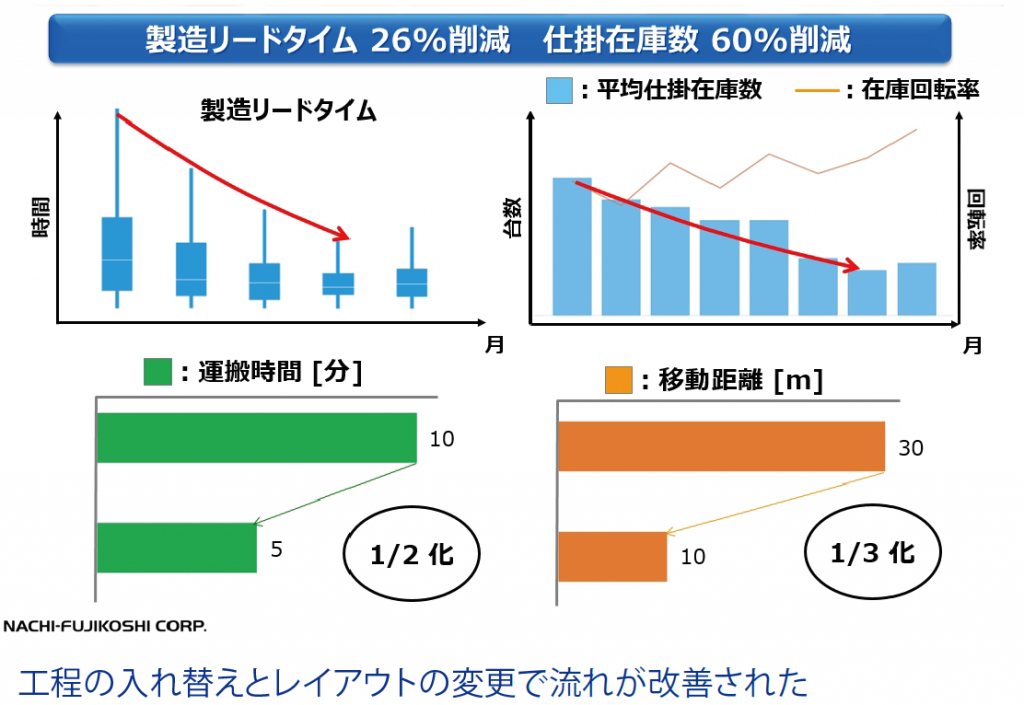
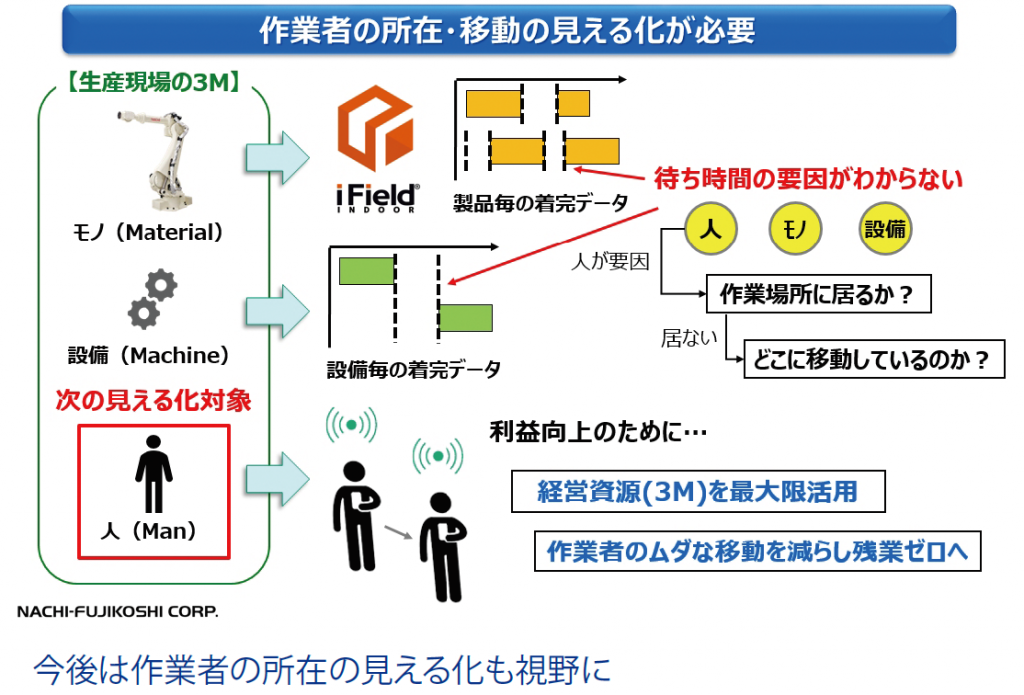
先頭工程から最終工程までの所要時間を改善前と比較したところ、平均リードタイムが26%、平均仕掛在庫数は60%それぞれ削減され、在庫回転率も改善されたことが確認された。また、現場のレイアウト変更によって、先頭工程から最終工程までの運搬時間が1/2に、移動距離も1/3に減少するなど、大幅な効率化が達成できたことが示された。
位置情報の取得により、仕掛品の滞留時間が定量的なデータとして明確になったことで、製造工程の俊敏な改善に結びついたことはもちろん、改善結果も見える化されるため、さらなる改善が図られることでPDCAサイクルを早く回すことが可能になった。
一方で、製品や設備ごとの着完データを見ると、工程の待ち時間が発生していることもわかった。新たな課題である待ち時間発生の要因を把握し、改善策を立案するには、作業者の所在や移動も見える化する必要がある。
「今後の利益向上のために、人の資源も最大限に活用していく必要があります。作業者の位置情報が見える化されれば、本来いるべき場所に人がいるのかいないのか、いないとすればその移動がどうして発生したのかも把握できます。作業者が無駄な移動をしているとすれば、そこを改善することで負荷も軽減される。こうした積み重ねで残業ゼロを目指していくことも重要になるので、次のステップとして屋内測位による作業者の位置情報把握に取り組んでいきたいと考えています」(臼井氏)
位置情報の取得により、仕掛品の滞留時間が定量的なデータとして明確になったことで、製造工程の俊敏な改善に結びついたことはもちろん、改善結果も見える化されるため、さらなる改善が図られることでPDCAサイクルを早く回すことが可能になった。
一方で、製品や設備ごとの着完データを見ると、工程の待ち時間が発生していることもわかった。新たな課題である待ち時間発生の要因を把握し、改善策を立案するには、作業者の所在や移動も見える化する必要がある。
「今後の利益向上のために、人の資源も最大限に活用していく必要があります。作業者の位置情報が見える化されれば、本来いるべき場所に人がいるのかいないのか、いないとすればその移動がどうして発生したのかも把握できます。作業者が無駄な移動をしているとすれば、そこを改善することで負荷も軽減される。こうした積み重ねで残業ゼロを目指していくことも重要になるので、次のステップとして屋内測位による作業者の位置情報把握に取り組んでいきたいと考えています」(臼井氏)
システムのポイント
- 仕掛品の工程進捗管理
- BLE BeaconとIoTゲートウェイを使った屋内測位技術を採用
- ボトルネック工程の把握
- レイアウト変更により製造リードタイム、仕掛在庫数を削減
お客様プロフィール
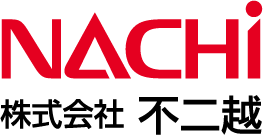
株式会社不二越( NACHI )
世界のあらゆるものづくりに貢献する総合機械メーカー。特殊鋼や工業炉などのマテリアル事業、工具・工作機械などのマシニング事業、ベアリング・油圧機器などの機能部品事業、エンジニアリング事業、そして本事例のロボット事業など多彩な技術を展開している。生産拠点は国内・海外にあり、ロボット部門は国内富山事業所内と中国工場の2拠点がある。
業種
製造業
目的
業務効率化
規模
数百台
関連サイト