WORKS
導入事例

タイ日野製造株式会社

タイ日野製造株式会社 様
「見える化」によるフォークリフトの台数削減がもたらした
従業員の意識改革
日野自動車タイ第一工場 屋内測位技術による工場内車両稼働「見える化」プロジェクト
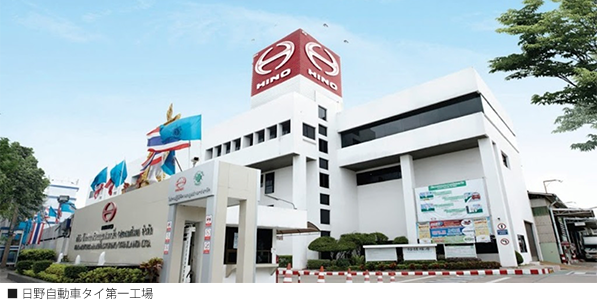
タイ日野製造株式会社工場では、荷物の積み下ろしや運搬で稼働しているフォークリフトや牽引車両の台数削減を目指していたが、詳細な車両稼働データがないことから取組は壁にあたっていた。こうした状況を打開するため、同工場では iField indoor( アイ・フィールド インドア) を導入し、工場内車両稼働「見える化」プロジェクトを実施し、10台の車両削減に成功した。車両の動きを分析した結果、動線の課題が見える化され、具体的な議論を進める事ができた。
また、本プロジェクトの成果は車両削減にとどまらず、工場内のひとりひとりの従業員に改善意識の醸成にもつながっていった。
iField indoor の導入で車両削減への取組が加速
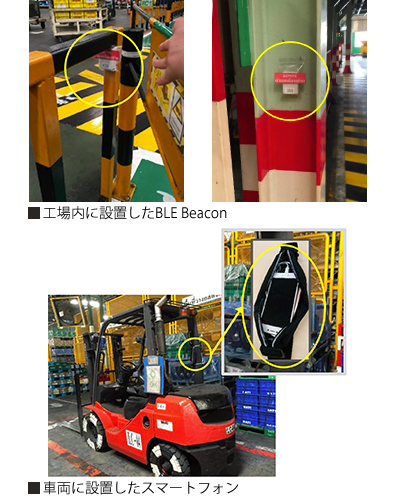
工場では従業員の安全確保や生産性向上のため車両台数の削減を進めていたが、ある一定のラインまで削減したところで、現場から「これ以上の削減は難しい」という声が上がるようになった。一方、同社で物流の効率化を担当する石塚・芥川氏は、「私たちマネジメント側から見ると、運転手不在のまま留置きされている車両があるなど、さらなる削減ができるように思えました」と話す。現場とマネジメント側の見解は異なるものの、具体的な車両の稼働データがなく、また荷捌きエリアと製造エリアでセクションが分かれている工場内では車両の動線把握も難しいため、それ以上の議論が進まないという状態だった。こうした課題を受けて、同工場では iField indoor を導入し、車両稼働のモニタリングを行うこととした。工場内にBLE ビーコンを、車両には受信のためのスマートフォンをそれぞれ設置し、対象期間内に対象車両の測位・センサデータを取得した。
工場が広域であるため、モニタリングは2期間に分けて実施され、合わせてBLEビーコン590個が設置された。取得したデータはビッグデータとして資産化し、分析結果から具体的な改善案を導き出す事ができた。分析は工場内を細分化する形でエリア設定を行ったうえで実施され、稼働率については、車両に取り付けたスマートフォンから、車両が動いているのか否かを判断し、求めた稼働率を車両ごと、日ごとに分 ける形で可視化した。また、車両がどのように移動してどのエリアに滞在していたのかについても分析を行っている。
分析結果をもとに現場メンバーとのディスカッション
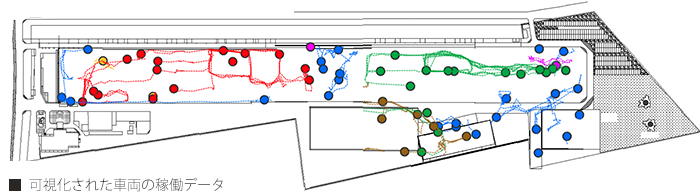
分析によると、稼働率は日による違いや日勤・夜勤による違いは認められなかったものの、牽引車はフォークリフトと比べて10ポイント程度低い稼働率であることが確認された。なぜ違いが出たのかを知るため、車両の稼働率を担当エリアごとに色分けして表示し、各車両がどのエリアに滞在していたのか、稼働の状態はどうだったのか、隣接エリアの車両の稼働率を併せてその車両の削減可否を、さらに削減できないのであればどういう理由があるのかを現場の担当に見てもらい、「回顧インタビュー」を実施した。
「稼働率を一覧化して色分けして、なぜ稼働率が低いのかをそれぞれの担当者とディスカッションしました。導線データを何回も再生して、『なぜここで止まっているのか』『なぜ ここに移動しているのか』といったことを具体的に確認して、一つ一つの作業の意味を確認できた」と芥川氏が語るように、これまで見えていなかった稼働の実態を把握することができたという。
「たとえば、フォークリフトと牽引車を一人の作業者が乗り換えて交互に作業していた例がありました。これは、過去の業務改善の中で、車両の稼働よりも省人化を優先した結果である事が分かりましたが、今現在の状況に照らして合理的なのかをスタッフと議論する良い機会となりました。また業務エリアをまたいで長い距離を動いている車両がいたことも把握できました」(石塚氏)
数字以上の定性的効果も
同工場ではこのプロジェクトの成果により、開始前に80台 近くあった車両のうち10台を削減することに成功し、更なる台数の削減も検討している。「定量化によりみんなが同じベースで議論ができて、水掛け論にならずに『削減しよう』という方向性を共有できた点が大きかったと思います。
各担当者がディスカッションを踏まえて、積極的にアクションを起こして迅速に削減を実現したことで、工場内全体の意識改革にもつながりました。見える化によって、従来であれば『避けられない』『プロセスを替えようがない』と決めつけられて改善案に挙がらなかったような課題に対しても、見直していこうという空気が現場にも生まれました。たとえば、製品出荷の際にクライアントのトラックが回ってくるのですが、これに対応するフォークリフトが3台あり、稼働率が非常に低いことがわかっていました。
しかし、このトラックはお客様が運用していることから調整が難しく、『仕方ない』と考えてしまい議論に上がることもありませんでした。それが今回のプロジェクトの成功により、現場にもトラック配送や積み下ろしの無駄を削減して効率化しようという意欲が生まれています。
また、工場内の牽引車の稼働率が低い問題についても、車両担当者から『生産ラインの稼働状況や部品の材料の検知を、センサーなどで行うなどIoT化を進めることで、ジャストインタイムが追及できるのではないか』という提案が出るなど、従業員全体に課題意識が醸成されたことも大きな成果でした」と石塚・芥川両氏が話すように、同工場では新たな課題の抽出とさらなる改善への機運が高まっている。
(2018年9月取材)
システムのポイント
- BLE Beaconを使った屋内測位技術を採用
- 車両台数削減に成功
- 従業員全体に課題意識が醸成
お客様プロフィール
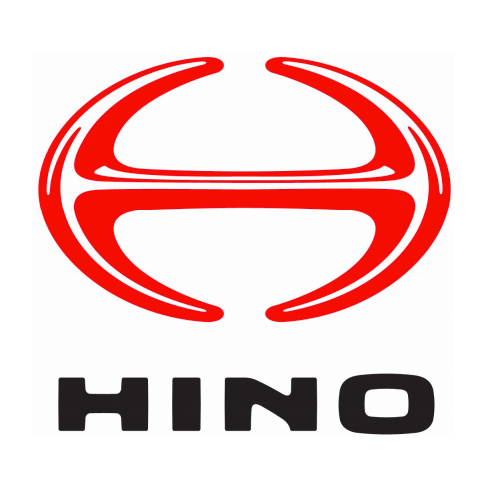
タイ日野製造株式会社
タイ日野製造株式会社 日野自動車初の海外製造会社として1964年に設立された自動車工場。バンコク郊外に3つの工場を持ち、トラック・バス完成車や自動車部品の生産を行っている。